Common Applications for Plastics Rotomolding in Today's Market
Common Applications for Plastics Rotomolding in Today's Market
Blog Article
Materials rotomolding, or rotational molding, is a manufacturing process that has acquired immense acceptance for the power to create resilient, hollow elements with outstanding precision. From large professional tanks to little custom components, this technique is known for their versatility and efficiency. Under, we'll explore the important thing great things about Pockets Plastics Rotomolding and why it's become a preferred answer for producing high-quality, hollow parts.
What's Plastics Rotomolding?
Rotomolding is a manufacturing process that involves heat plastic material inside a revolving mold. This allows the molten plastic to coat the inner surfaces of the shape consistently, making empty areas with a smooth structure. The effect? A product that's not just durable but additionally amazingly adaptable, providing endless programs across industries.
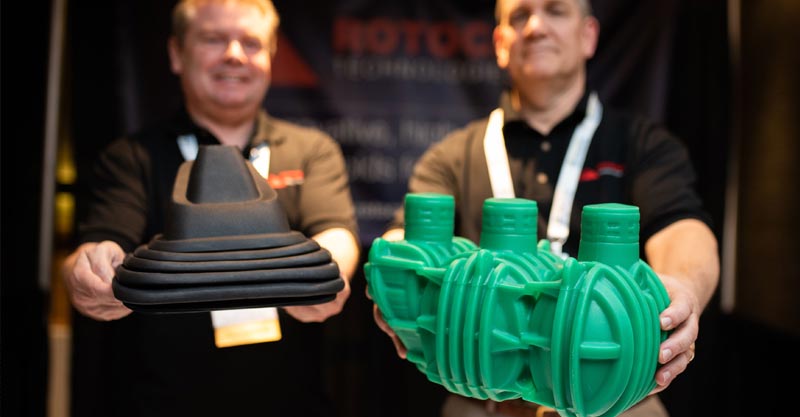
Crucial Great things about Parts Rotomolding
1. Strength and Durability
One of many standout benefits of materials rotomolding may be the unmatched toughness it offers. Rotomolded components are created to endure serious problems, including major influences, tough weather, and compound exposure. That energy makes rotomolded parts suitable for applications in industries like automotive, agriculture, and construction.
The seamless, single-piece construction also contributes to the structural reliability of rotomolded products. Unlike other practices, you can find number stitches or flaws, lowering the danger of pauses or leaks.
2. Cost-Effective Generation
Rotomolding is highly cost-effective, specially when creating big or complex useless parts. The procedure needs relatively minimal tooling charges compared to different manufacturing strategies, such as for instance injection molding or hit molding. This helps it be particularly suited to small-to-medium manufacturing runs without sacrificing quality.
Moreover, the capacity to create elements with regular wall width reduces substance spend, optimizing cost-efficiency also further.
3. Style Flexibility
The usefulness of rotomolding opens the entranceway to extremely customizable designs. Whether it's complicated patterns, undercuts, or various wall thicknesses, rotomolding allows makers to turn even the most complicated styles in to reality. That flexibility is important for industries that need accuracy and versatility in their components.
Further modification options contain distinctive surfaces, stuck positions, and even multi-layered parts for added efficiency or strength.
4. Lightweight However Powerful
Rotomolded elements achieve an ideal stability between fat and durability. The useless construction reduces product application, ensuring items stay lightweight while maintaining their architectural strength. This is specially good for pieces such as outside gear, tanks, or playground structures, wherever simple transportation and installation are crucial considerations.

5. Eco-Friendly Production
Rotational molding can be generally celebrated for the environmental benefits. The method effects in small substance waste, as plastic components can frequently be recycled or recycled. Moreover, suppliers may use eco-friendly components to align with sustainability goals. This jobs rotomolding being an significantly appealing option for agencies seeking to reduce their environmental impact.
Why Plastics Rotomolding Stands Out
Pockets rotomolding has revolutionized the production of resilient, empty parts by offering a unique combination of power, cost effectiveness, and design flexibility. By leveraging this technique, producers can provide supreme quality areas that meet the particular needs of various industries while encouraging an eco-conscious way of production.
If you are looking for a production procedure that provides easy toughness and irresistible detail, rotomolding may be the answer.
Report this page